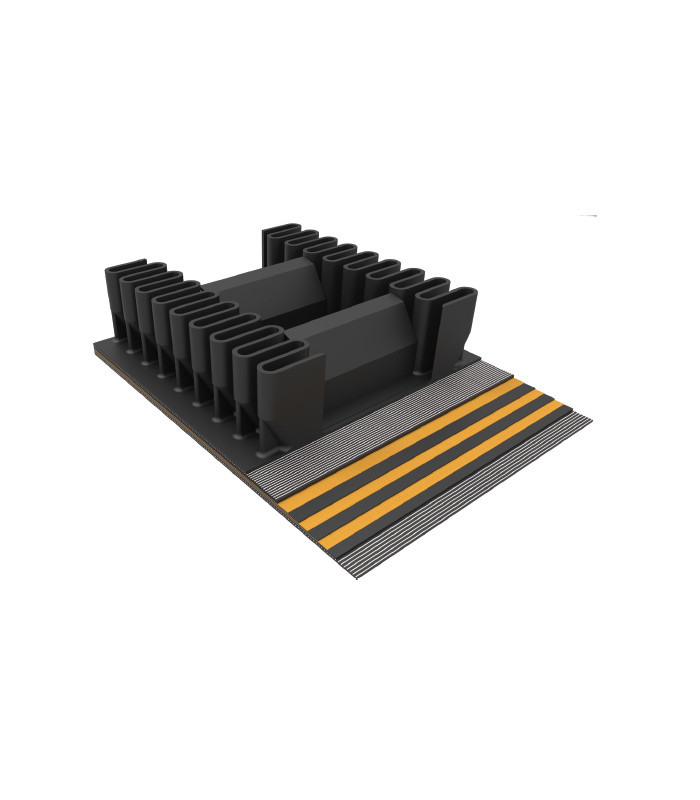
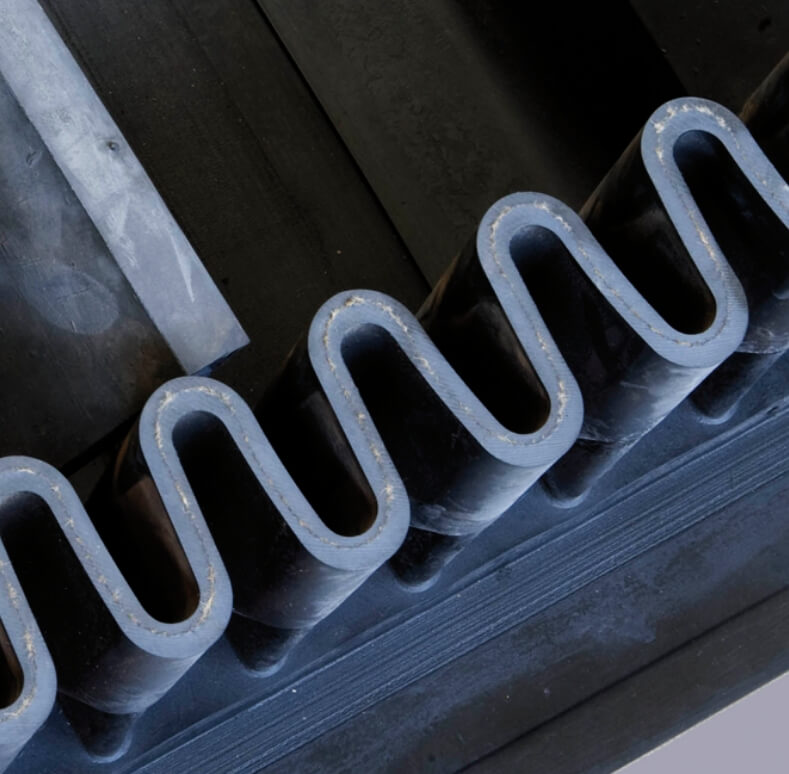
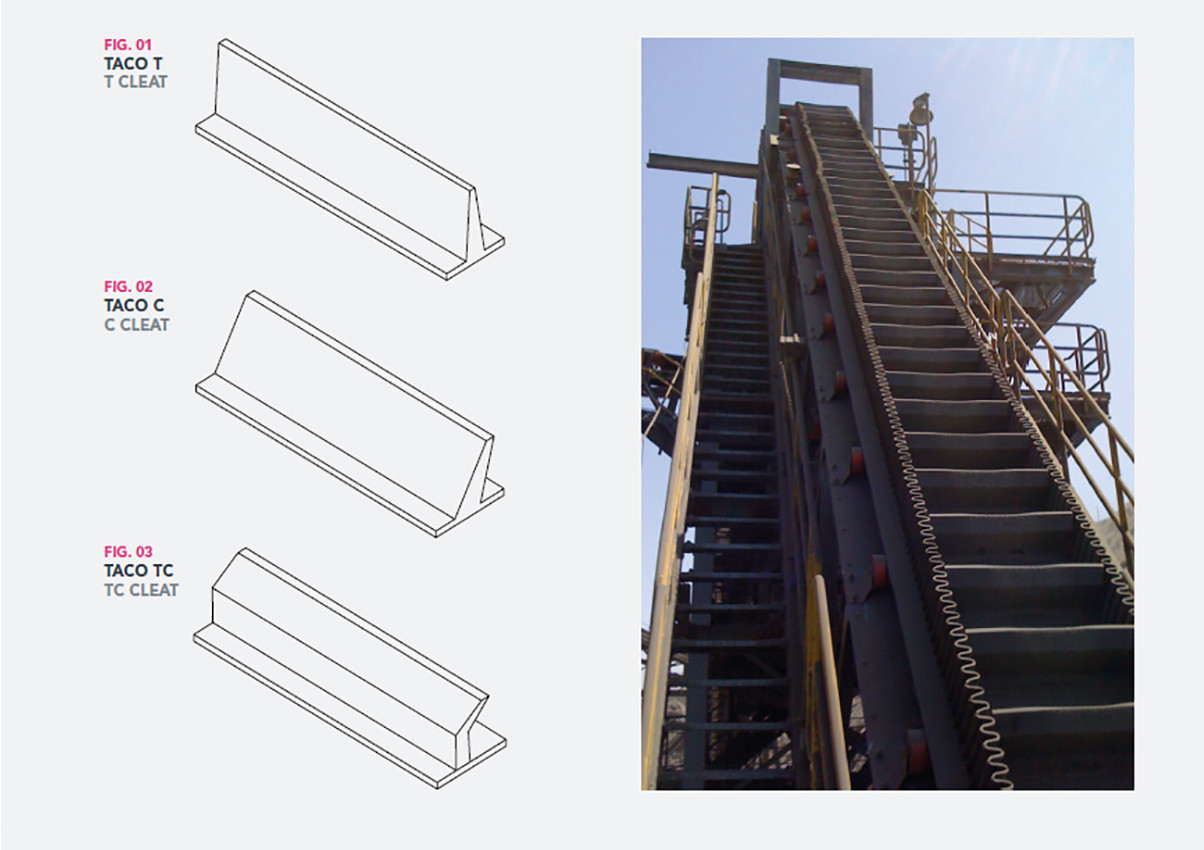
KAUBORD consists of a base belt, to which two sidewalls made of hot-vulcanized corrugated rubber are added on the edges, providing security, stability and durability. They can also include transversal rubber cleats, also fixed to the base belt and the sidewalls. Compartments are thereby formed, like a continuous bucket elevator. Hot vulcanization enables a significantly better adherence than cold vulcanization, eliminating the risk of the elements stuck to the belt coming off.
This kind of conveyor belt was developed for uses requiring elevation angles of over 45º, even vertical carrying, or for cases in which the fluidity of the material means it could fall off the edges on a regular plane. The other distinctive element is that as these belts are exceedingly flexible, they can change from horizontal to inclined or vertical carrying and vice versa in the same facility. There are other significant alternatives in construction, such as carrying different materials at the same time, with no risk of them getting mixed up, by setting up intermediate containing walls. In small facilities where no inflexion is required due to changes in the slope, standard belts can be used with no transversal rigidity, with the most appropriate edges and cleats for the kind of transport in question.
The general characteristics
for this kind of conveyor belt are as follows:
Within this range of casings, there are standard types with one or two transverse weaves, which can be rigid, where appropriate, which favors applications such as bucket elevators, belts with flat installation resistant to impacts and longitudinal tears (log transport, etc.), and with the additional advantage of being able to be applied in the entire range of resistances and routes of the conventional multi-layer EP textile belt. It presents a significant improvement when it comes to breaking resistance and high transport lengths since, in addition to not having a significant cost difference, it allows the lengths of the tensioners, the diameters of the drums and the energy consumed by the installation to be reduced.
These belts are mainly used in facilities with pronounced slopes, even of 90º, in diverse sectors, such as for example underground mining (e.g. coal), coal-fired and biomass power plants, the extraction industry, iron and steel, metal, port facilities and ship to ship loading, cement plants, quarries, the food industry (e.g. cereal silos), fertilizers, extraction for tunnel building, and preparing sand for foundries and recycling plants.