This website uses cookies so that we can provide you with the best user experience possible. Cookie information is stored in your browser and performs functions such as recognising you when you return to our website and helping our team to understand which sections of the website you find most interesting and useful.
Cement plants
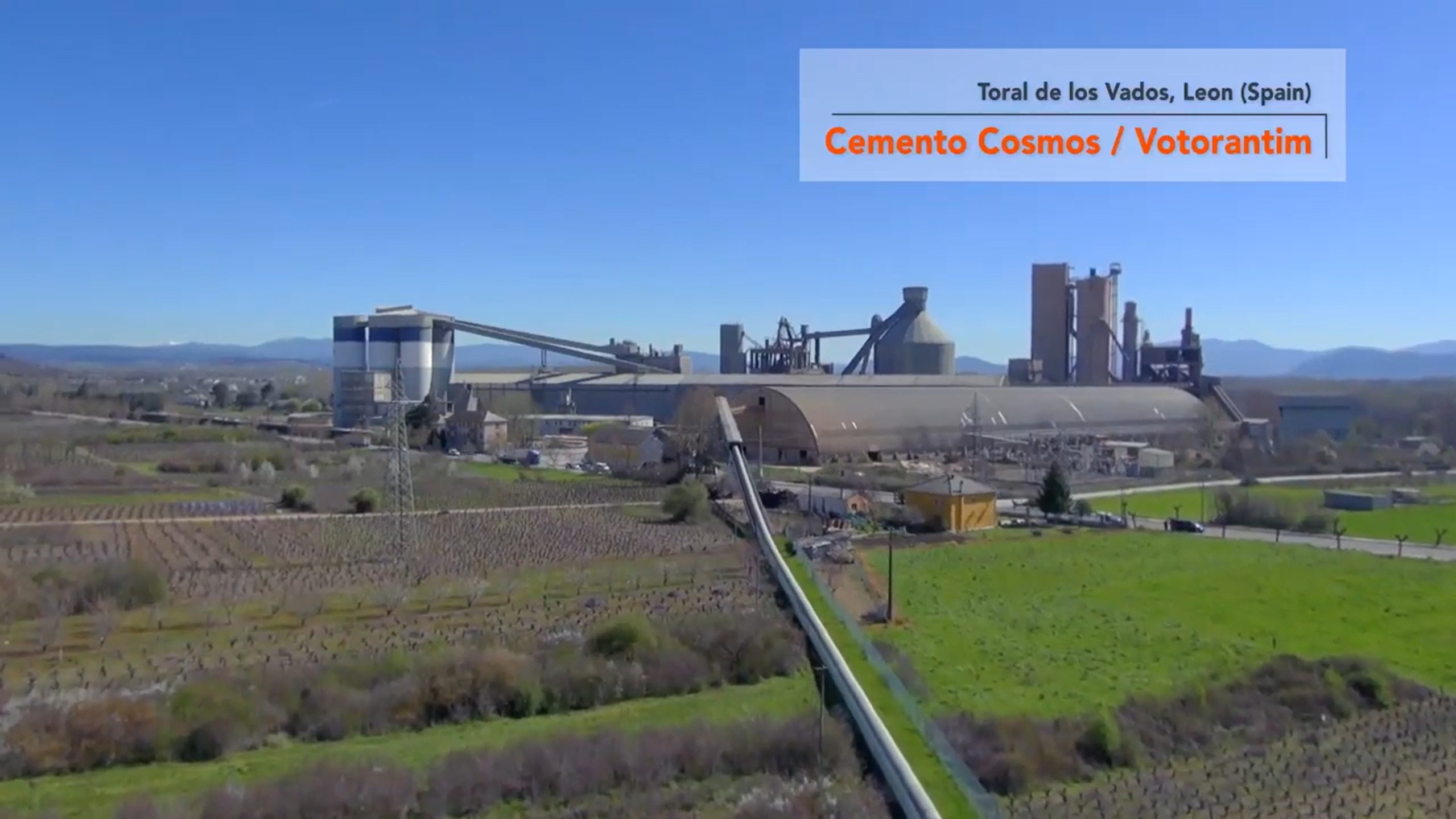
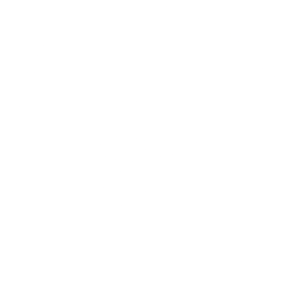
QUALITY AND DEVELOPMENT IN THE CEMENT INDUSTRY
The cement industry involves a complex and demanding work environment which requires the best quality in order to obtain a finished product in an efficient and profitable way. There are various different kinds of material applications and transport systems in the cement industry in which rubber conveyor belts play a very important role.
The specific development of rubber in our laboratories and the experience we have acquired as conveyor belt suppliers for the cement industry means we are in a position to provide a specific product and guarantees for our clients in the sector.
We have achieved the capacity to adapt our rubber qualities and belt reinforcements to each use of cement. Our goal is that you no longer have to worry about the performance and status of the conveyor belt throughout its useful life, or be concerned about unexpected and costly interruptions to production.
We are very much aware of the importance of conveyor belts in a cement plant, which is why our R&D&i department works on finding solutions from extraction to cement packaging. When the material being carried is very hot and abrasive, it is essential for cement plants to have the right transport system for each specific process; and this is why we have put together our rubber and compound conveyor belt catalogue for all the processes in cement manufacturing.

Anti Cut NoRip
The belt at the start of cement production should be able to work in extreme situations. In the extraction process the rocks are ground and carried by a Kauman belt capable of bearing powerful impacts and large stones with sharp edges. For this purpose Kauman has developed a special reinforcement for textile and steel belts called Anti Cut NoRip®, which consists of a breaker inserted into the upper cover of the belt, usually selected as BF125HE, or depending on the fall distance and material, a breaker that is more resistant than BF125. Kauman recommends the use of this breaker in the process before the first grinding in cement plants.
With a Kauman Anti Cut NoRip®, the belt carcass is protected from impacts as it absorbs the effect of the fall when carrying limestone or clay. The Anti Cut NoRip® also avoids the longitudinal tearing of the carcass by sharp materials.
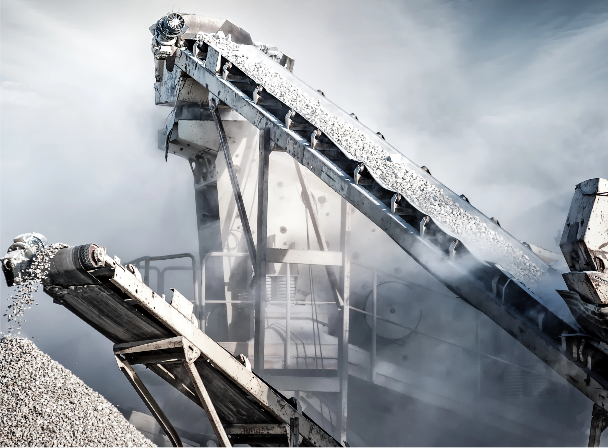
Anti Cut (AC) rubber compoundt
Given that rubber can tear when carrying sharp-edged materials in this process, Kauman recommends a specially formulated rubber to avoid cutting and tearing. We have therefore formulated and developed an anti-cut (AC) rubber compound for the first process in material extraction, when the material frequently cuts and tears the rubber covers. The compound’s minimum resistance to tearing is 25 Mpa, while the abrasion specifications are a minimum of 110 mm, which means the compound is highly resistant to cutting and compensated with good resistance to abrasion. The AC cover compound can be included on any of our textile or steel belts.
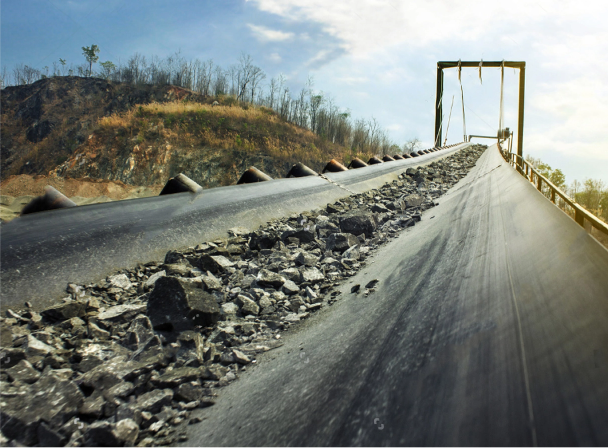
Kausteel
The materials extracted from the quarry are ground and then fall onto a belt or series of belts which go to the limestone warehouse. It is critical to select the right kind of conveyor belt at this point, depending on the distance and the size of the material.
This carrying section normally covers long distances, and so it is essential to select a long-lasting belt which does not require constant maintenance or the frequent replacement of parts. The most frequently used belts in this process are KAUSTEEL®, with a steel mesh.
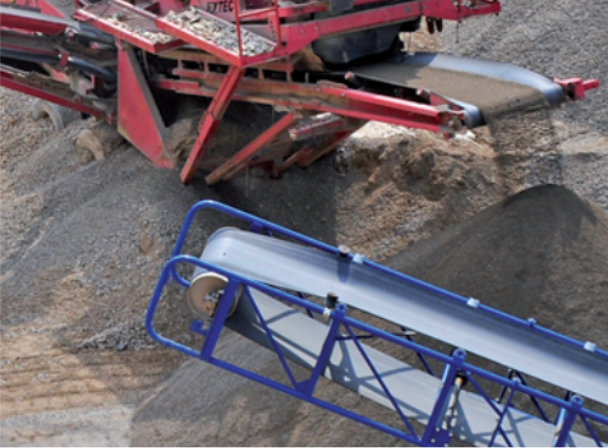
Kaustrong
At Kauman, thanks to our experience and as an alternative, we use an EPP fabric textile belt because of the difference in weight, price and its resistance to heavy materials. he material still has sharp corners and large dimensions in this phase, and so Kauman recommends KAUSTRONG®, an EPP textile belt capable of covering large distances with very low elongation, less weight than a steel belt and whose structure absorbs impact 4 times better than normal reinforcements. In short, the main reasons for using this kind of belt in grinding transport are:
- Low elongation.
- Better belt alignment than with a steel mesh or EP belt.
- High resistance to heavy materials, longitudinal cutting and tearing.
- High absorption of impacts.
- Less weight.
We can manufacture the KAUSTRONG® belt with one or two layers; the most resistant construction is an EPP2500 / 2 with a belt resistance of 2500 N / mm and which can be manufactured with a width of 2200 mm.

Kaupipe
At some cement plants, when ground limestone is carried a great distance from the mine to the plant, special precaution is required due to the location of the belts and to avoid dust and dirt escaping. In such cases our clients use a tubular conveyor belt. Kauman recently launched KAUPIPE®, an EP conveyor belt which is circular in shape. This belt’s main advantages for the cement industry are:
- The elimination or reduction of transfer points, and so there is less maintenance and less time is used.
- A flexible design with adjusted horizontal and vertical curves.
- Better adapted to irregular land.
- Covered transport, protecting the material from rain, wind and snow.
- It prevents material from falling and generating dust in the plant, and so it protects the environment.
KAUPIPE® can be adapted to a carrier with a diameter of 600 mm, capable of carrying a great amount of material. Please contact our engineers to arrange a visit and a personal study of your particular case.
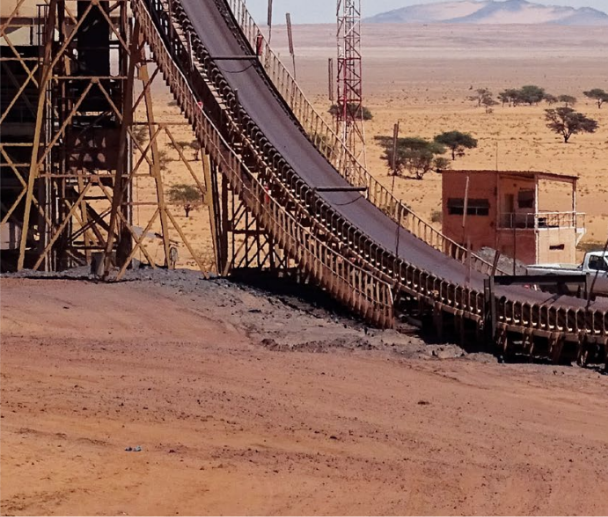
Pyroprocessing includes the preheating tower and the kiln that heats up the ground raw material (known as “raw meal”) and sinters it in the clinker. This “raw meal” is then taken to the pyroprocessing phase via a bucket elevator belt.
A bucket elevator is normally used to carry smaller grain material, such as “raw meal” before calcination and in finished cement storage silos before shipping.
Kauman has shown its reliability in hundreds of cement plants in ongoing operation, such as the feeding of silos and the preheating tower.
Kauman is specialized in designing and producing a complete focus on the bucket conveyor belt to guarantee continuity of performance and the useful life of the elevator belt.
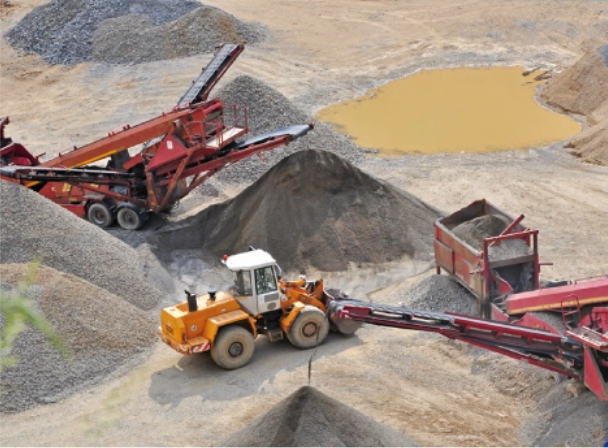
Kaulev
Our rubber bucket elevator conveyor belt for the cement industry is called KAULEV®. It is conceived for bulk fine material which requires great transport capacity, up to 2500 m3 / h, in order to reach this level of performance. Kauman uses its Fleximat®, a steel mesh in the warp and rigid cords in the weft. The main advantages of steel mesh cords are improvement under compression, low elongation and excellent rubber penetration, in addition to the weft cords which provide a powerful barrier against longitudinal cutting and tearing.
The KAULEV® belt is designed for heights over 200 m, and to achieve a resistance in the steel mesh of up to 4000 N / mm (areas with no wires to fix the buckets, if necessary). For hot material in bucket elevators, depending on the cement plant’s process, Kauman has developed an EPDM rubber compound that is resistant to heat and enables the permanent carrying of material at temperatures of up to 160ºC in bucket elevators.
Steel belts for resistances of up to 4000 N / mm. Heights of over 200 metres. Temperatures of up to 160ºC for permanent materials. Minimum elongation is 0.3% at maximum work load, even on long belts.
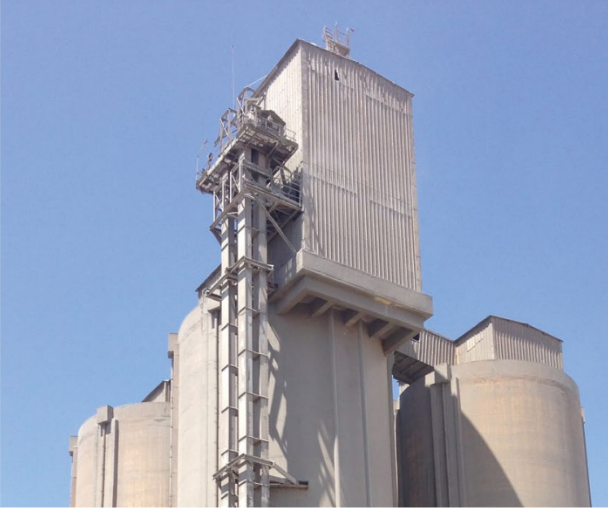
THE IMPORTANCE OF COVER COMPOUNDS IN THE CLINKER PROCESS
At Kauman we are very much aware of the importance of selecting the right cover compound for each belt in each process, which is why we are presenting our improved cover compounds, resistant to oil, grease and high temperatures.
OIL AND GREASE RESISTANT RUBBER COMPOUNDS
During the clinker combustion process, materials such as coal and oil are used as energy sources, and so the conveyor belt cover should be protected from oil and grease. Kauman has developed various resistant conveyor belts which are adapted to different temperatures and the state of the material in the burning process. Depending on the material and the content of oil and grease, it is important to select the right cover compound. The main properties to take into account are the working temperature and the temperature of the material, the kind of oil and grease, the need for an anti-flame belt and the abrasion of the material. Please get in touch with us to find out about the right cover compound for your processes.
TEMPERATURE-RESISTANT RUBBER COMPOUNDS
In order to transport the hot clinker after the combustion process, the conveyor belt should comply with the temperature requirements for carrying hot materials at temperatures of up to 200ºC. Kauman guarantees the protection of the belt by providing special heat-resistant covers for materials at up to 225ºC. We divide our heat-resistant compounds into 3 different categories: T15, T18 and T20.
Kauman’s compounds for the cement industry can be adapted to different circumstances, depending on: – The size of the material particles – The speed of the belt – The length of the belt- The environmental temperature. We would recommend inspecting the temperature of the clinker and the transport combinations at each stage in the plant and the size of the particles in order to choose the right cover. However, it is important to differentiate between the temperature of the belt surface and the temperature of the material being carried. The temperature of the material at different plants can vary in accordance with the above-mentioned circumstances.
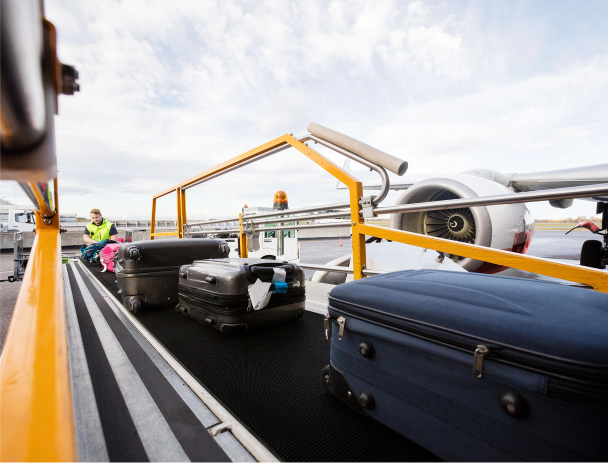
Kaucenter
When the clinker is taken to the warehouse or finished product mills, any material which falls from the belt can be very problematic; dust is highly volatile and if it falls on the belt it can get into the rollers and pulleys and damage the belt’s components. In many cases, an unaligned belt is the reason why, in addition to spillage, damage is also caused to the edges of the belt, the splices and the structure. To avoid these situations, Kauman, in collaboration with experts in the cement industry, launched its self-centring conveyor belt under the name of KAUCENTER®.
TheKAUCENTER® is an EP textile or steel belt with an additional transversal rigid weft with the same width as the central belt roller. The difference in flexibility between the centre and the edges of the belt is what maintains it permanently centred and well adapted to the three rollers. Thanks to the characteristics of the self-centring belt, it is the perfect solution for belts which often become unaligned. Among other problems, this can lead to a loss in load capacity, material falling together with the blockage systems, thereby reducing operating time and wearing the edges of the belt. Kauman recommends, in general, for storage in mills at a great distance or to avoid the falling of dust, a KAUCENTER® belt with a BF800RE Breaker to considerably increase the belt’s transversal rigidity and avoid any transversal movement. Please contact our engineers to make the calculations for your specific belt.
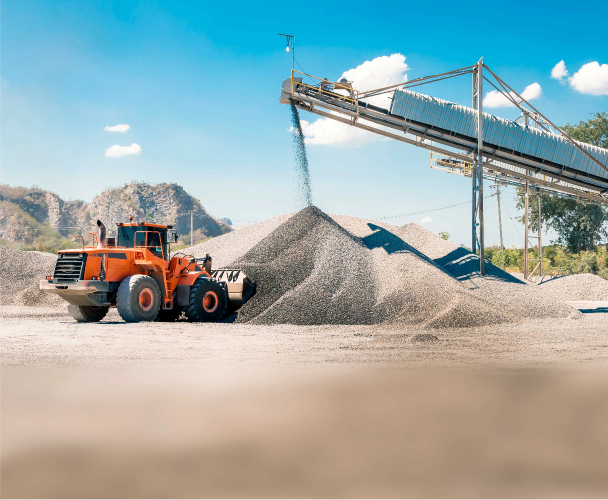